Dirty Work for Clean Energy
Below ground at a wind farm is just as exciting as what is above. Installing kilometres of medium-voltage cable is a complex business for structural engineering experts such as Schulte-Perk. We paid a visit to the building site.
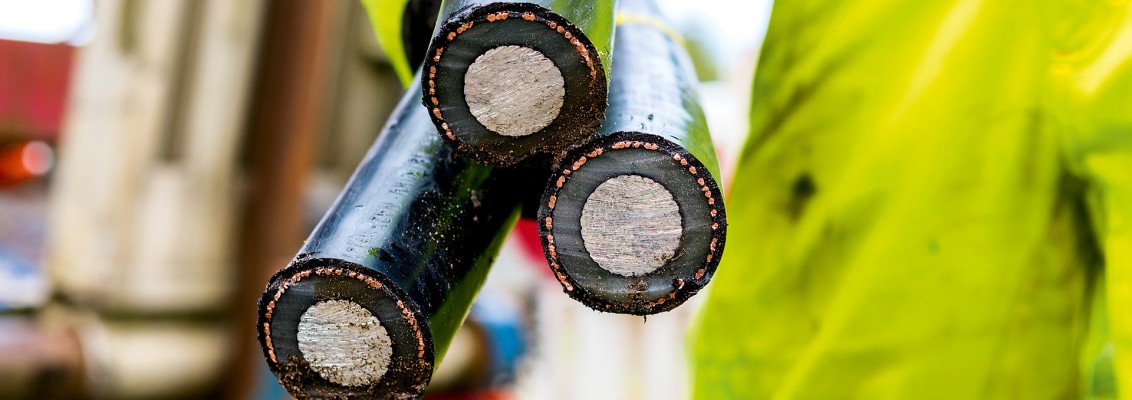
The job of adding six additional wind turbines to the wind farm in Damme (Lower Saxony) is in full swing. A tractor towing a 15-metre-(50-foot)-long cable-laying machine turns off the road on to a dirt path across from Borringhauser Moor Windpark. The 30-tonne colossus comes to a halt alongside a ditch. Dieter Thomas, project manager at Schulte-Perk‘s pipeline construction division, is waiting there. Three drums of NA2XS(F)2Y single-core, medium-voltage cable are sitting on the cable-laying machine. This cable is particularly robust thanks to its resilient polyethylene outer sheath that can easily withstand the tough mechanical stresses encountered during installation and operation. Additionally, it‘s longitudinally watertight, which means water in the cable cannot spread out alongside the conductor and no moisture can make its way through the sheath to the inner conductor.
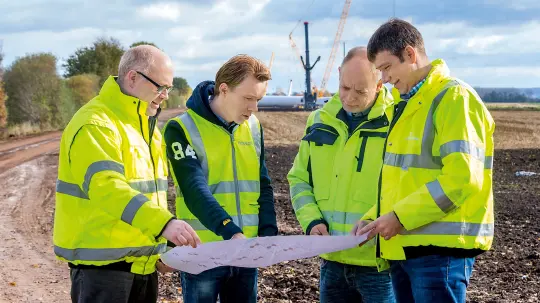
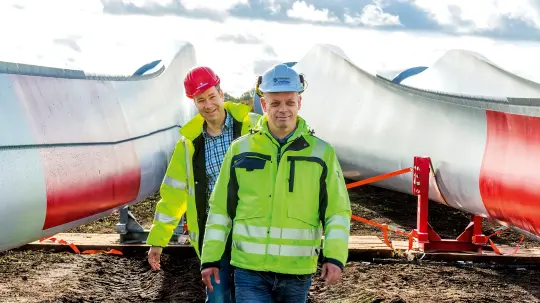
MINIMALISED TRANSMISSION LOSSES
Schulte-Perk workers unwind the single-core, medium-voltage cable from each drum and bundle the three cables together to form a cable system. They lay the bundled cable, metre by metre, next to stretches of the ditch that are easily accessible to heavy machinery. An excavator follows behind the workers and lifts the three-strand bundle carefully into the 120-centimetre (4-foot) deep and 60-centimetre (2-foot) wide ditch. In places where the excavator can’t access, Schulte-Perk‘s men have to use pure muscle to lift the cable into the ditch. “We are working on two sections of the route here at Borringhauser Moor. Each section contains the cable system for three of the six wind turbines. The NA2XS(F)2Y medium-voltage cable we are using has a cross section of 150 square millimetres (300 kcmil). The cable system needs to be split in half to minimise power losses during the four kilometre (2.5 mile) journey. The longer the section, the greater the losses,“ explains Thomas. The strands of the two cable systems meet at the coupling station. From here on, the electricity is fed through a single cable bundle to the transfer station, which is in the direct vicinity of the transformer station. “For this section we had to use three single-cores with cross sections of 630 square millimetres (1250 kcmil). This solution allows the power to be transported from all six wind turbines and we are able to keep conduction losses to a minimum,“ says Thomas. The transfer station belongs to the transformer station that is operated by a regional utility company, which feeds the power into the AC grid.
DEEP BELOW GROUND
The Schulte-Perk team has already laid a couple hundred metres. Plastic conduits and a copper wire lay beside the black, medium-voltage cable in the ditch. “The copper wire grounds the system and prevents potential differences that develop between the coupling station and the wind power plants,“ explains Thomas. The conduits protect fibre optic cable that will be pulled through later. This cable will transmit control commands to and data from the wind turbines for remote maintenance and evaluation by the wind farm‘s operator.
Whenever the installation route crosses a road, stream, water pipe or some other piece of existing infrastructure, things start getting complicated for the Schulte-Perk construction engineers. “We have to dig deep below the ground at that point,“ says Thomas. To cross a road, for example, Thomas and his colleagues have to resort to wash boring. First of all, a drill head cuts its way through the ground. A back reamer, or hole opener, then widens the tunnel to the required diameter. Things start to get tricky when the tunnel goes around a bend, which might be anything between ten and fifty metres (33 and 165 feet) long. Varying soil consistency along the installation path is also an issue, which is why the tunnel needs to be stabilised by mixing bentonite into the drilling water. This is just one of Schulte-Perk‘s many engineering skills that are in high demand for jobs like this.
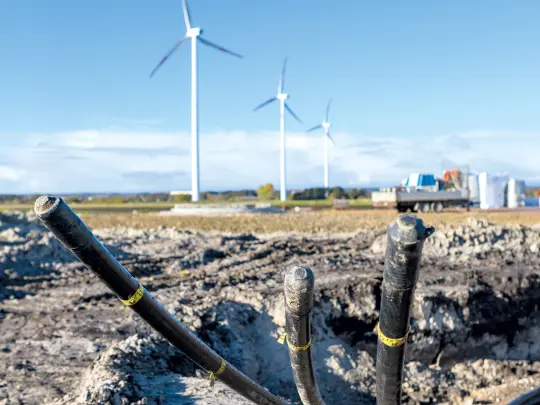
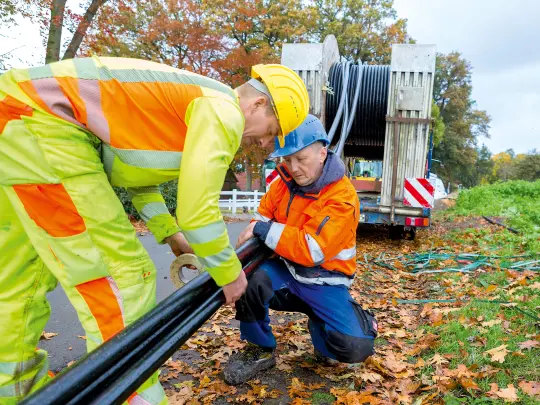
QUALITY TEST PASSED
Dieter Thomas and team walk along the dirt path and check the other construction work going on at the wind farm. In one field, red and white rotor blades are lying on the ground as they wait to be put into operation. The wind turbine towers have been erected and the underground work is almost finished. Soon after, the turbine’s nacelle will be mounted. Later, a high-voltage test of the medium-voltage cables will be carried out. This involves loading every cable section with a test voltage of 54,000 volts for one hour even though the cables only have to transmit a maximum of 30,000 volts during normal operation. The medium-voltage cable with the larger cross section already passed this test back in November. “Before we fill in the ditch, we have to be absolutely sure everything‘s working properly,“ says Thomas. “We guarantee that the cables we installed have been tested according to the technical regulations before operations start. This is something the wind parks operator can rely on”.
UNTIL THE ROTOR BLADES ARE TURNING
As expected, the cables passed the test and have been transporting the power generated by the six new wind turbines, as planned, since December 2016. Berthold Klatte, CEO of WPD Windpark Damme GmbH & Co. KG, is delighted that the turbines are finally running. They are able to generate 55 million kilowatt hours a year, making them as efficient as the 15 existing turbines. “It was rather hectic on the construction site last December, but the commissioning, which was carried out by Siemens, went just as smooth as Schulte-Perk‘s underground work,“ explains Klatte. “It‘s really amazing how fast things went once work was finally allowed to begin. We started the planning and approval procedure back in 2008, but the project‘s existence was put in jeopardy when a sea eagle nested near the farm,“ he recalls. “The compromise was to drop four of the original 10 wind turbines. This allowed us to maintain sufficient distance to the nature reserve.“ The sea eagle is now undisturbed, and clean electricity is being generated by the wind farm for homes in the area.
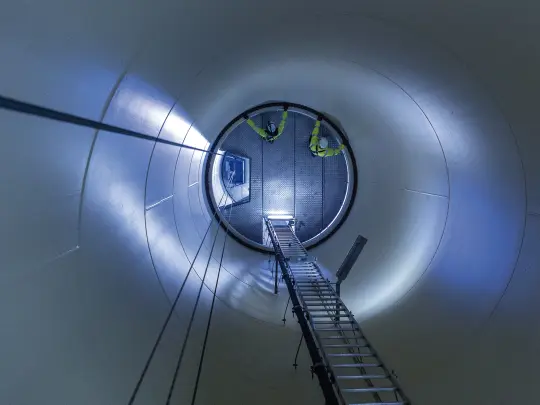
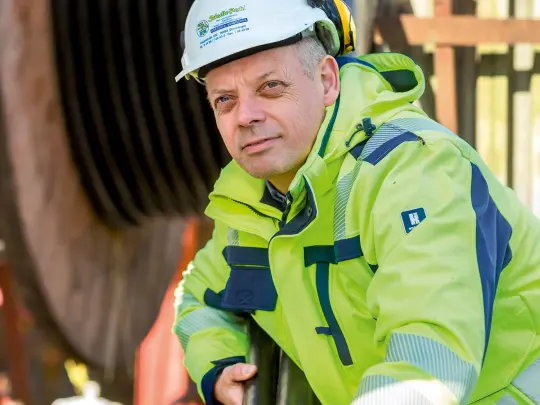